The Complex Journey of Development a New F1 Car
The development of a new Formula 1 car is a multifaceted process that combines cutting-edge
technology, engineering prowess, and extensive testing. As teams strive for competitive advantage
in the high-stakes world of Formula 1, the research and development (R&D) process has become
more critical than ever. This message delves into the key stages of how F1 teams design and
develop a new car, highlighting the intricacies involved in this fascinating journey.
1. Concept Design
The journey begins with concept design, where the team evaluates their performance from the
previous season and considers new technical regulations introduced by the FIA (Fédération
Internationale de l’Automobile). This phase is crucial as it lays the foundation for the car’s
overall design philosophy. Engineers and designers brainstorm ideas, considering factors
such as aerodynamics, weight distribution, and power unit integration.
During this phase, the team often utilizes computational fluid dynamics (CFD) software to
simulate airflow over the car’s body. This allows them to identify potential aerodynamic
improvements without the need for physical prototypes. The insights gained during these
simulations help inform the design direction, ensuring that the car is optimized for both
speed and efficiency.

2. Engineering Design
Once the conceptual framework is established, the focus shifts to detailed engineering design.
This stage involves creating precise specifications for every component of the car, including
the chassis, suspension, and power unit. Using advanced computer-aided design (CAD) software,
engineers draft intricate designs that adhere to the technical regulations while pushing
the boundaries of performance.
Collaboration between different departments is crucial at this stage. Aerodynamics experts work
closely with mechanical engineers to ensure that the design maximizes downforce while
minimizing drag. Additionally, the integration of various systems, such as electronics and
cooling, is meticulously planned to ensure optimal performance.
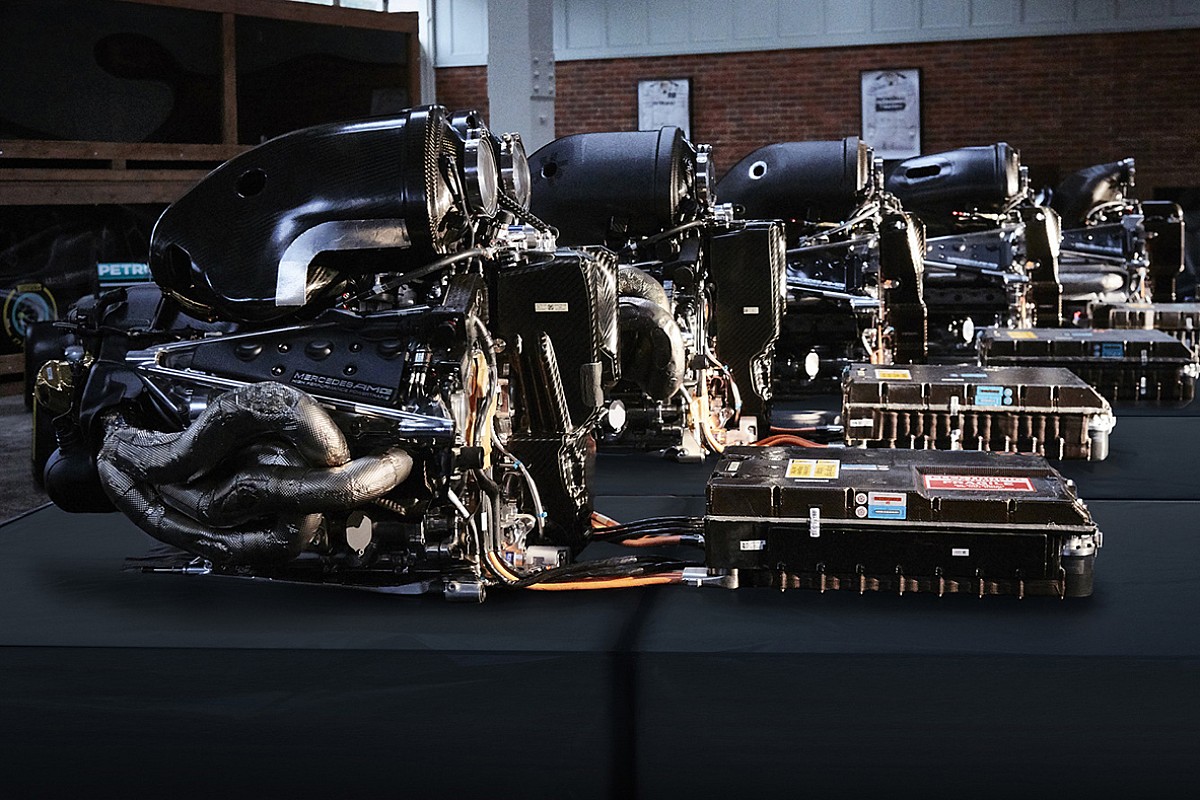
3. Prototype Manufacturing
With detailed designs in hand, the next step is to create prototypes. These prototypes serve
multiple purposes: they allow for initial testing of aerodynamics, weight distribution,
and component interaction. Teams may produce full-size models or scaled-down versions for
wind tunnel testing.
The manufacturing process requires precision and attention to detail, as even minor imperfections
can significantly impact performance. High-quality materials such as carbon fiber and
lightweight alloys are commonly used to construct various parts of the car, balancing strength
and weight.
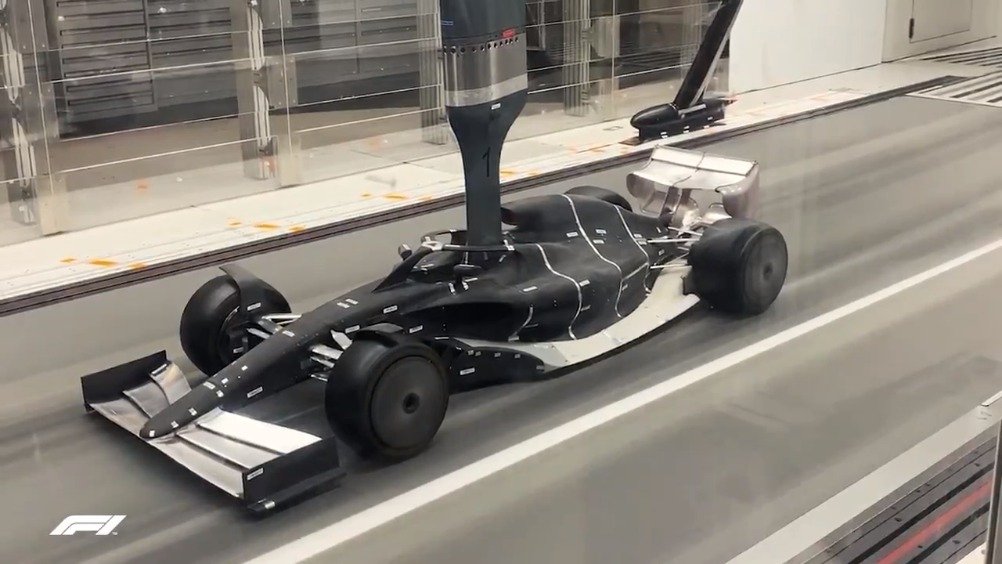
4. Wind Tunnel Testing
Wind tunnel testing is a cornerstone of F1 car development. It allows teams to
evaluate the aerodynamic performance of their prototypes in a controlled environment. By
placing the car in a wind tunnel, engineers can analyze how air flows around the vehicle
at different speeds and angles.
This phase often reveals insights that can lead to design tweaks, such as altering the shape
of the front wing or adjusting the rear diffuser. Engineers may iterate through several
versions of the car, making gradual improvements based on the data collected during testing.
The objective is to achieve an optimal balance between downforce and drag, crucial for both
high-speed performance and cornering ability.
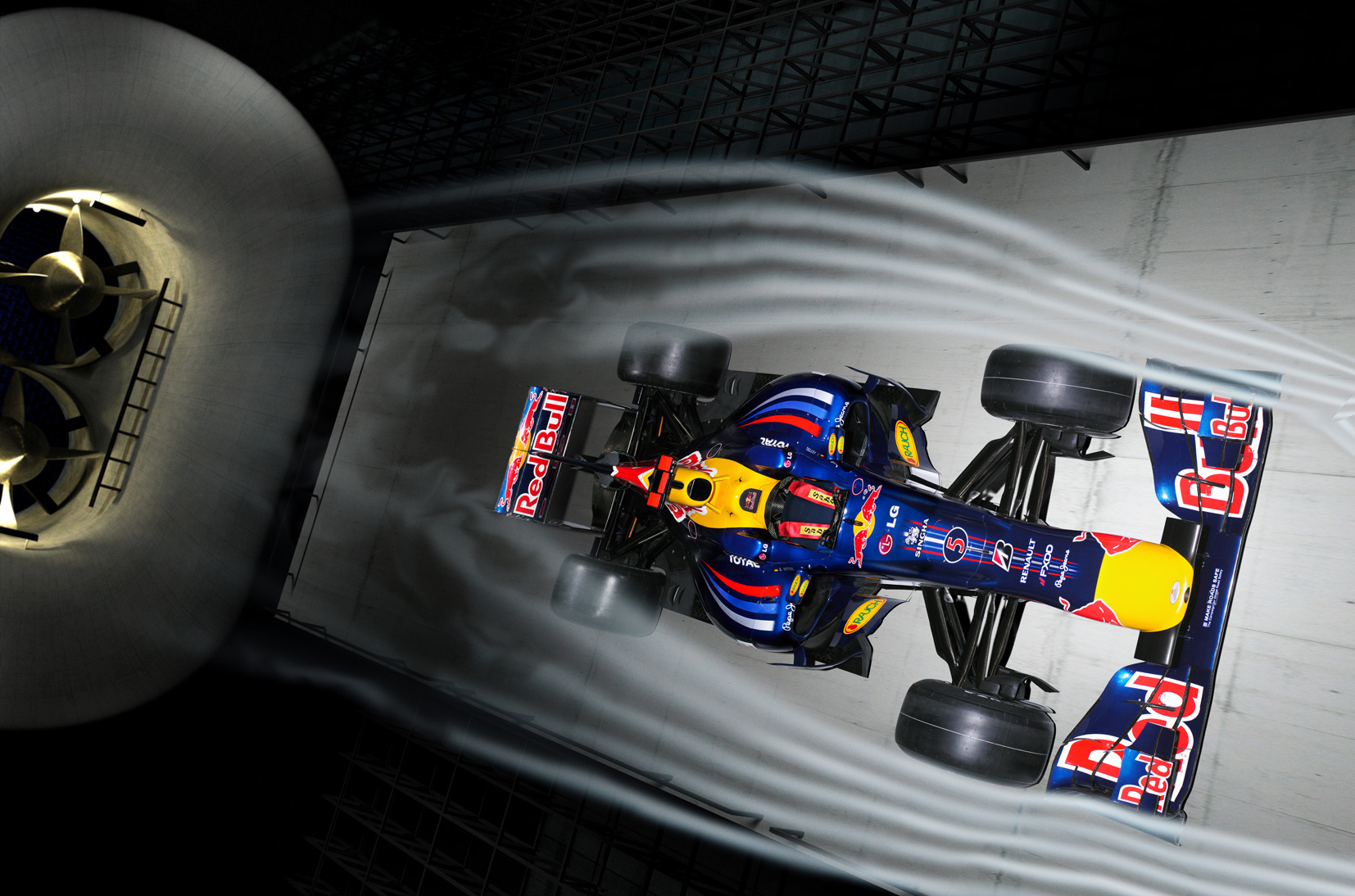
5. Track Testing
After extensive wind tunnel testing, teams move to on-track testing, where they can
evaluate the car’s performance under real racing conditions. This stage is vital,
as it allows drivers to provide feedback on handling, braking, and acceleration. The
integration of driver input is essential; what works well in a simulation may not always
translate to the track.
During testing, teams monitor various parameters, including tire performance, fuel
consumption, and engine reliability. This data helps engineers understand how the car
behaves in different conditions, from varying temperatures to different track surfaces. By
conducting these tests over multiple days, teams can fine-tune the car’s setup for
optimal performance.
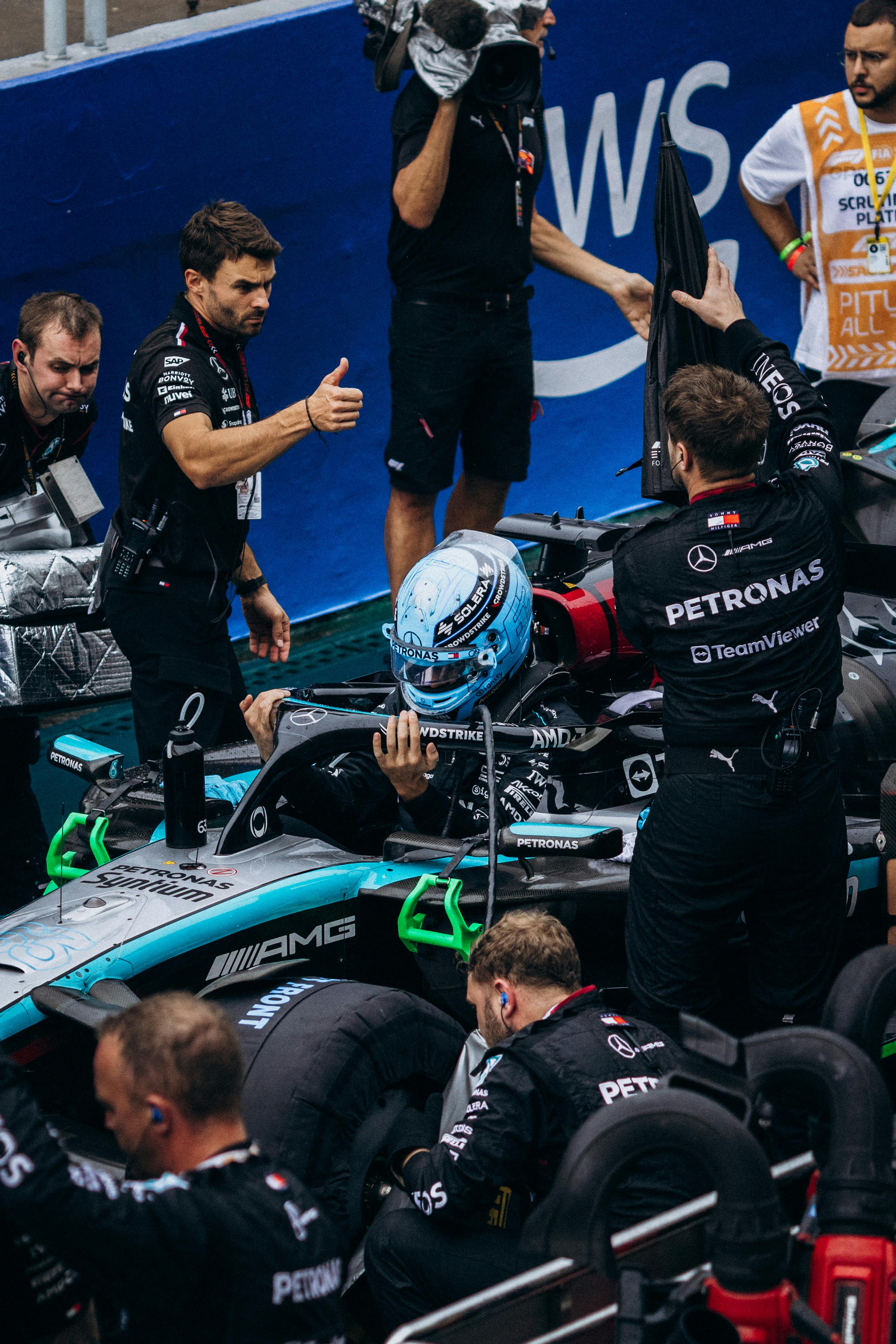
6. Data Analysis
The collection and analysis of data are ongoing throughout the development process. Teams use
advanced telemetry systems to gather real-time data during both wind tunnel and track testing.
Engineers analyze this data to identify patterns and areas for improvement.
Data analysis involves looking at aspects such as tire degradation, lap times, and fuel
efficiency. By comparing performance across various configurations, teams can pinpoint
the most effective setups and strategies. This data-driven approach ensures that decisions are
based on empirical evidence rather than intuition alone.
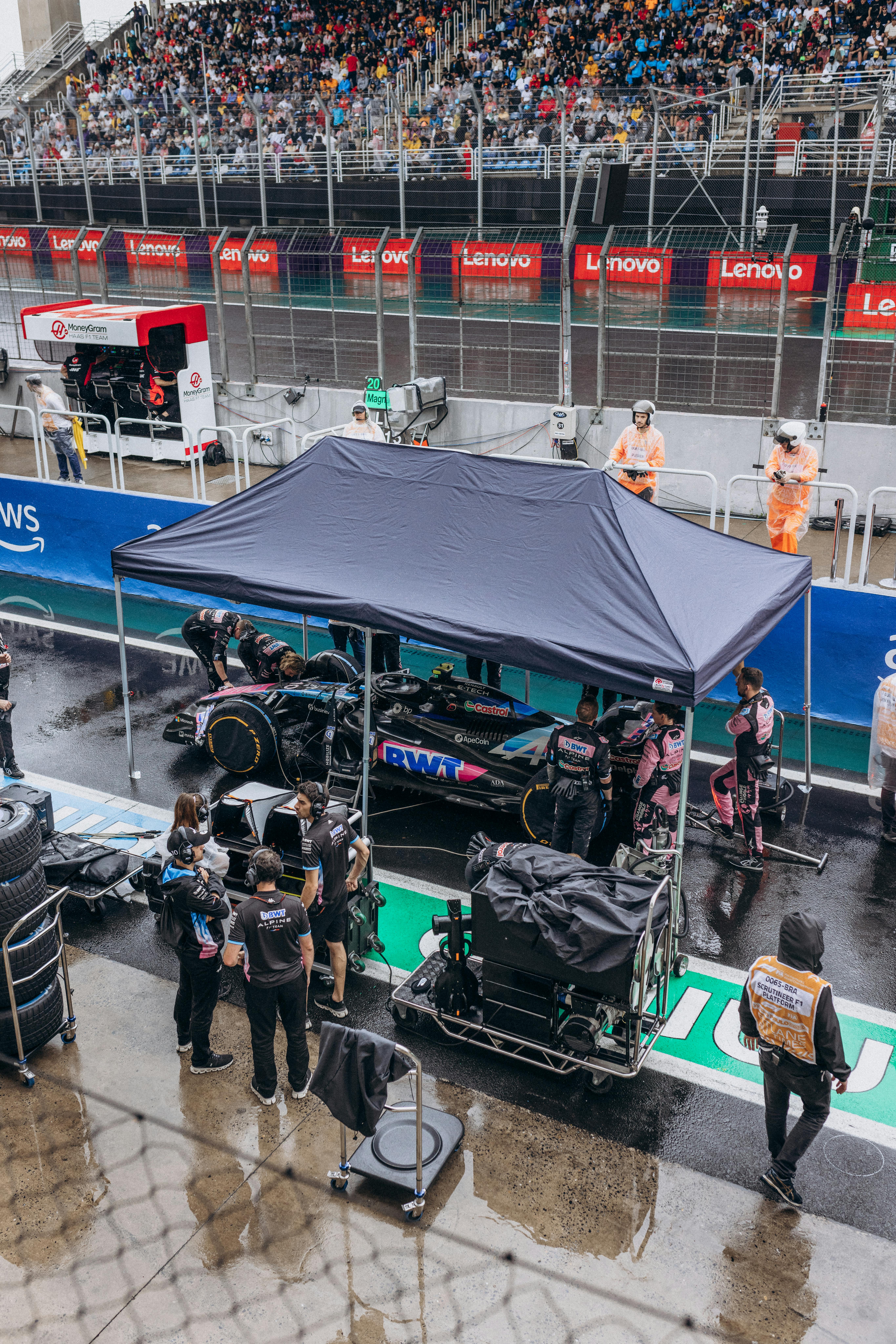
7. Final Adjustments
After extensive testing and data analysis, teams make final adjustments to the car. This
phase is about refining the design to ensure that it is race-ready. Changes might include
optimizing weight distribution, enhancing cooling systems, or making minor adjustments to
aerodynamics.
Collaboration between the engineering team and drivers becomes even more critical at this
stage. Drivers’ feedback on handling and performance is invaluable, as they are the ones who
will push the car to its limits during races. The goal is to ensure that the car feels intuitive
and responsive, allowing drivers to maximize their performance on the track.
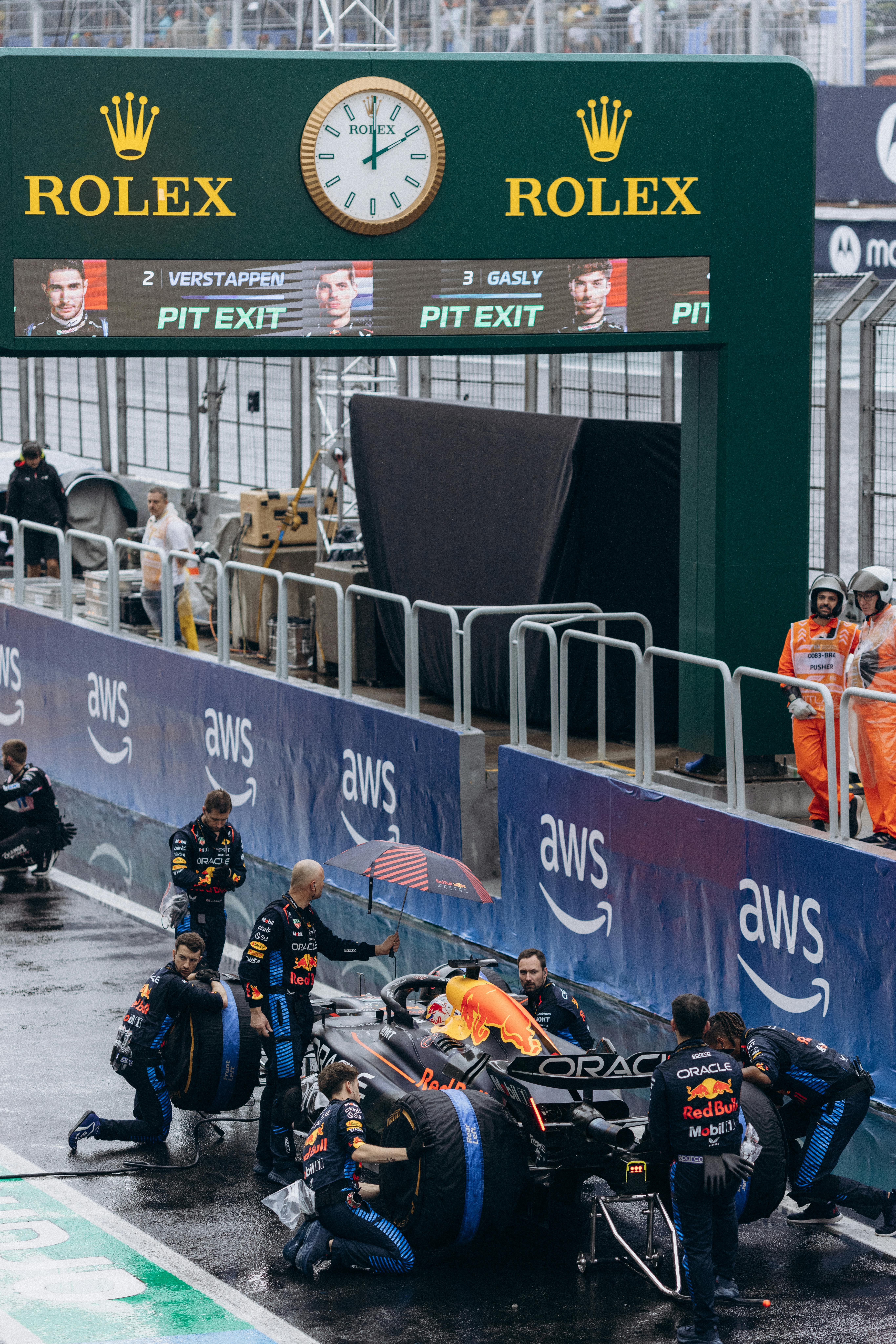
8. Production and Maintenance
Once the design is finalized, the team begins the production phase. This involves
manufacturing multiple units of various components to ensure that they have sufficient
spares for the race season. The production process must adhere to strict quality control
standards to ensure reliability and performance.
Throughout the season, ongoing maintenance and updates are essential. Teams continuously gather
data during races, and this feedback loop informs future design changes and improvements. The
iterative nature of car development means that teams are always looking for ways to enhance
performance, even mid-season.
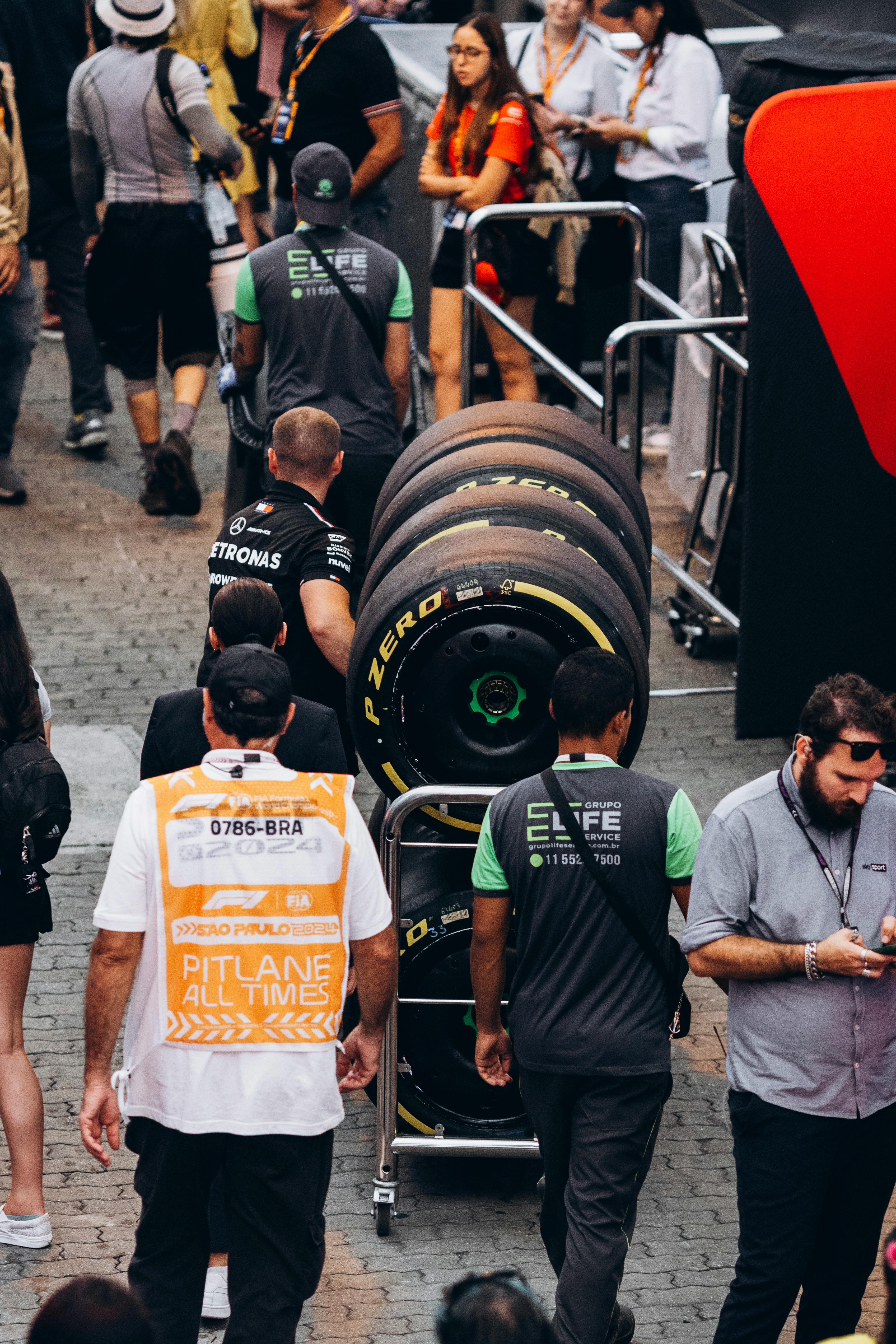
Conclusion
The development of a new Formula 1 car is a complex and meticulous process that involves a
blend of creativity, engineering, and scientific analysis. From initial concept design to on-track
testing and final production, each step is crucial in creating a competitive machine capable
of performing at the highest level.
As teams continue to innovate and push the boundaries of technology, the evolution of F1 cars
will undoubtedly remain a captivating aspect of the sport. The pursuit of speed, efficiency,
and reliability ensures that each season brings fresh excitement and fierce competition,
keeping fans and teams engaged in the relentless quest for victory.